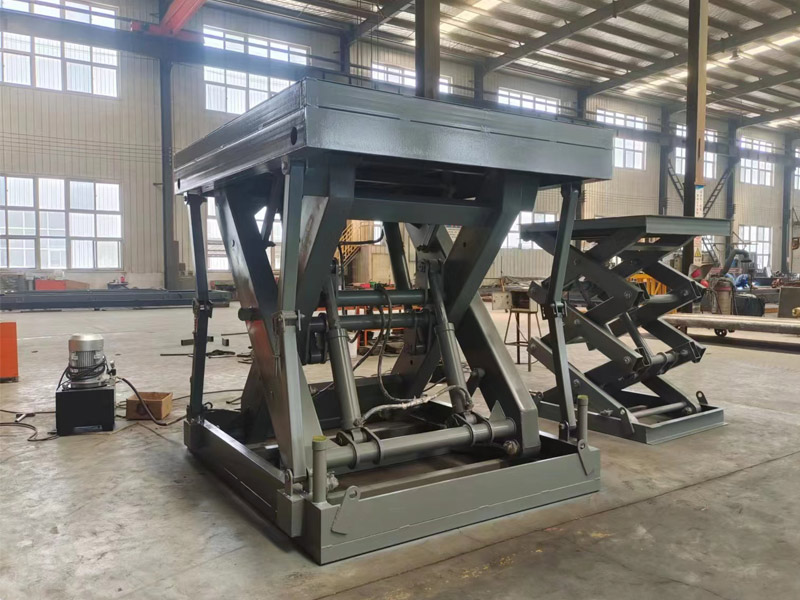
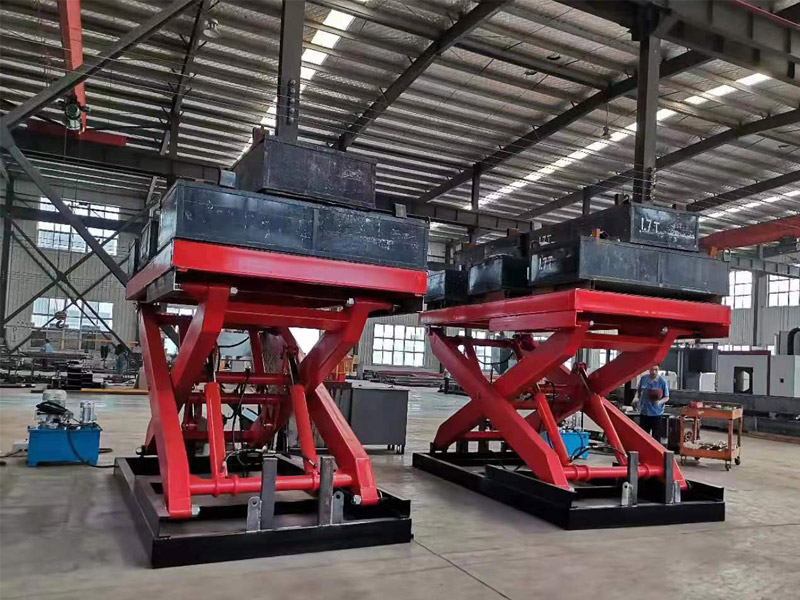
The customization process of a cargo lift mainly includes the following steps:
1. Determine the requirements. It is necessary to provide detailed information including the size, weight, and required lifting height of the required goods, so that designers can configure the equipment and set parameters according to actual needs.
2. Select a manufacturer for on-site inspection and confirm the details of the design plan. The selected manufacturing enterprise conducts a comprehensive evaluation of product solutions and prices based on specific usage scenarios and requirements, and ultimately selects suitable suppliers to ensure product quality and reliability of after-sales service.
3. Negotiate with manufacturers to develop detailed contract terms and quotations to meet customer requirements such as special specifications, and conduct cost accounting to ensure their reasonableness while ensuring the operational efficiency and stability of the equipment.
After completing the sample acceptance, we can officially start shipping, installation, and debugging. Through training, we will enable customers to master the operating skills proficiently and fully utilize the machine to improve work efficiency.
Due to the fact that the device is used in special industries, customers may need to provide relevant certification documents to improve entry efficiency and enhance safety precautions. In summary, in order to achieve the smooth implementation of the above aspects, it is necessary to have an understanding of the market situation and relevant standards in order to successfully implement effective cost control and meet the personalized needs of customers. The above information is for reference only. If you have any further questions, you can consult relevant personnel for answers.